The Air Clear Advantage is total customer support for your Air Pollution Control Equipment, from user friendly operating and maintenance manuals to online monitoring providing virtually effortless system operation.
Technical support after the sale and more importantly, after the warranty period, is critical. So along with building and testing the highest quality equipment possible, Air Clear offers you the support you need to minimize downtime.
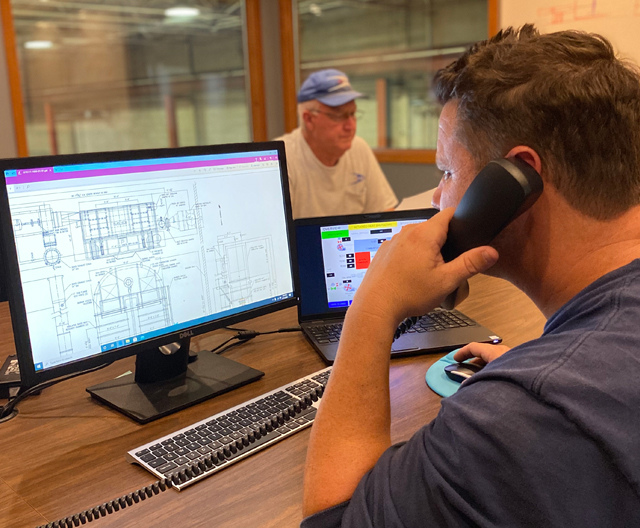
Air Clear integrates modems into our customers’ control systems, so that our engineers can diagnose and adjust the operating status of installed Air Pollution Control Systems.
Air Clear is continuously finding new and more effective ways to integrate modems into our customers’ control systems, so that our engineers can diagnose and adjust the operating status of your system whether it is in Bangkok or Baltimore.
Where Staff is limited, Air Clear offers optional maintenance contracts. These flexible agreements can include remote monitoring, service and maintenance, spare part inventory and training of local contractors as needed.
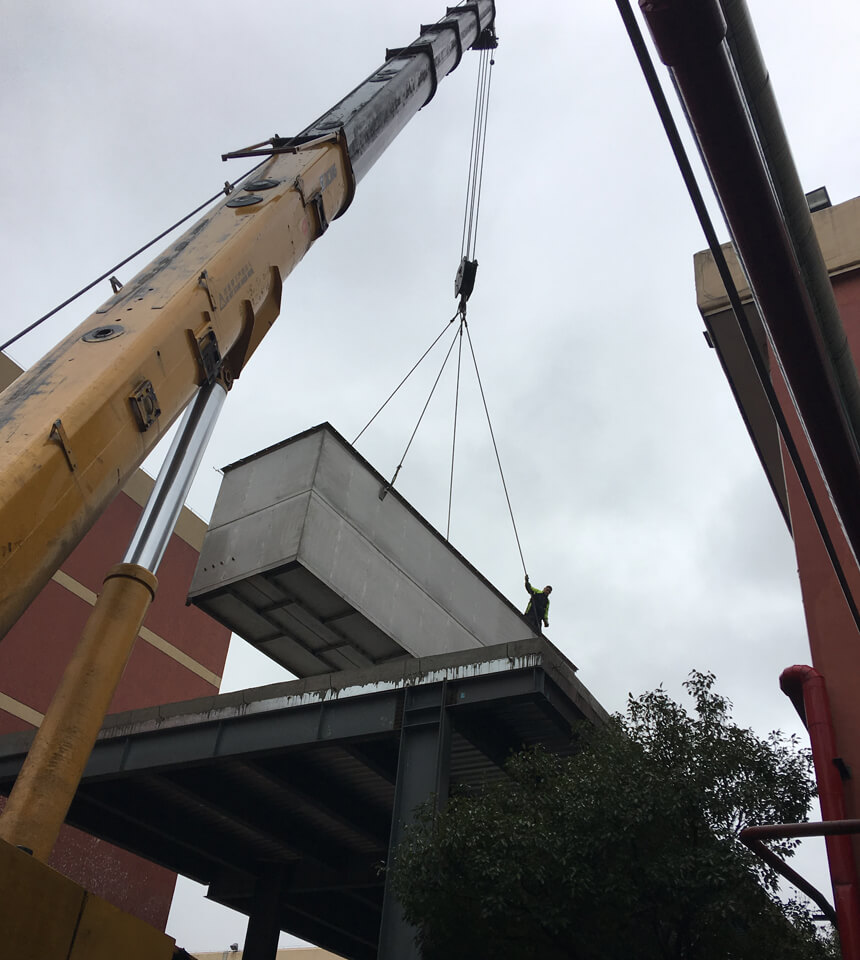
FiberBed Filter Unit gets installed in Ningbo, China.
Project
Management
Air Clear’s Project Management Teams insures all involved understand the interrelationship between system and process.
Air Clear embraces the fundamental elements of top project management from design and project schedules, written documentation, drawing management, procurement, inspection, testing and shipping. We assist in installation, startup and training, provide engineering support and offer tailored maintenance agreements. Our “Vigilance” guarantees that you get the right system, built to your exact specifications, with every effort made to keep tomorrow in mind for what we build today!
Quality Control
Air Clear’s air pollution control equipment is manufactured by Air Clear personnel at our Elkton, Maryland facility. This allows rigorous quality control and confidence to totally guarantee our systems performance.
The Air Clear approach to quality control is a unique blend of internal and external review to assure engineering and fabrication of the highest precision. Our customers are always welcome to inspect our workmanship during the manufacturing process.
Since we fabricate in-house, we have complete control over both quality of the equipment we are engineering as well as production scheduling. We also have the chance to pretest components supplied to us by outside vendors. Before any Air Clear projects are released for construction, our engineers, design team, sales and production people must sign off on the entire system. Upon completion, our customers are invited to witness a rigorous shop test of their equipment. This test greatly reduces startup and training time.