Client: POSCO Engineering & Construction Co. Ltd (Pocos Steel)
Location: Pohang, S. Korea
Process: Color Coating Line
Background: Pocos Steel has (3) three high-volume color coating lines which emit 200 to 500 Kb/hr of VOC emissions which must be controlled. Initially, Pocos Steel installed Recuperative Thermal Oxidizer which utilized a 60% Thermally Effective Shell & Tube Heat Exchanger to reduce fuel input. However, even with the use of the 60% heat recovery, the fuel consumption was too high. Pocos Engineers wanted to install a new Regenerative Thermal Oxidizer (RTO), but there were (3) three concerns. First, they needed the new equipment to achieve a higher DRE. The Thermal Oxidizer had a 95% DRE but the goal was to be at least >98% with 99% preferable. Second, were the varying solvent loads which range from 200-500 kg/hr. These loads would cause an RTO with 95% TER to overheat and shut down when the solvents exceed ~350 Kg/hr. Third, the final size of the Regenerative Thermal Oxidizer (RTO) was much larger than the existing Thermal Oxidizer so finding a location for the Regenerative Thermal Oxidizer (RTO) would be challenging.
Solution: Air Clear Engineers suggested a new Regenerative Thermal Oxidizer (RTO) engineering design which would be located on the outside will of the production area set back into an unused loading dock area. The RTO engineering design would utilize (3) three chambers to allow for a purge chamber. The purge would allow for DRE greater than 99%. Air Clear incorporated structured media to achieve 90% TER as well as a High Temperature Bypass Valve (HTB) to control high temperature loadings. Most operating modes require 0% fuel input to the RTO System as VOC concentrations were sufficient to maintain required combustion temperatures.
Replacing an old Oxidizer with an RTO
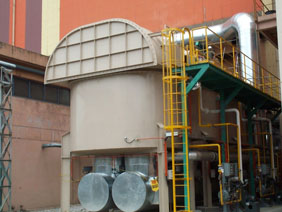