Regenerative Thermal Oxidizers – Air Clear Regenerative Thermal Oxidizers (RTO) Manufacturer of Custom Designed Systems. Thermal Regenerative Oxidizers (RTO) systems are the most energy efficient and cost effective solutions for the reduction of Volatile Organic Compounds (VOCs) and odorous air emissions. The primary function of the Thermal Regenerative Oxidizer is to destroy the VOC contaminants in the exhaust coming out of a process. The operation of the Thermal Regenerative Oxidizer is based on the principle of combustion. The process of combustion is the most commonly used method to control emissions of organic compounds. Regenerative Thermal Oxidizers (RTOs).
The Air Clear Thermal Oxidizers remove Hazardous Air Pollutants (HAPs), VOCs, and odorous emissions discharged from industrial processes. The Thermal Oxidizers achieve process emission destruction through the means of high temperature thermal oxidation. In doing so, it is converting the pollutants to carbon dioxide and water vapor while recovering the thermal energy generated to reduce operating costs. Due to the regenerative thermal oxidizers high thermal energy recovery, they are well suited to applications with low VOC concentrations, yet high waste stream flow rates. The typical operating temperature range for an industrial RTO system is from 815°C (1,500°F) to 980°C (1,800°F). Thermal Oxidizer – EPA
How the Air Clear Regenerative
Thermal Oxidizer (RTO) Unit Works
VOC and HAP laden process gas enters the Regenerative Thermal Oxidizer (RTO) unit through an inlet manifold where valves (butterfly or poppet) direct this gas into energy recovery chambers. The process gas and contaminants are heated in the ceramic media beds as the gas moves toward the combustion chamber.
Valves alternate the airflow direction into the media beds to maximize energy recovery within the oxidizer. The high energy recovery within these oxidizers reduces the auxiliary fuel requirement and saves on operating costs. The Air Clear RTO unit achieves high destruction efficiency and self-sustaining operation with no auxiliary fuel usage at low concentrations.
Air Clear Regenerative Thermal Oxidizer (RTO)Once the VOCs in the process exhaust have been treated in the oxidizer combustion chamber, the hot purified air releases thermal energy as the organics is oxidized, reducing fuel use. The hot ‘cleaned’ gas passes through the outlet media bed. The outlet bed is heated and the gas is cooled so that the outlet gas temperature is only slightly higher than the process inlet temperature.
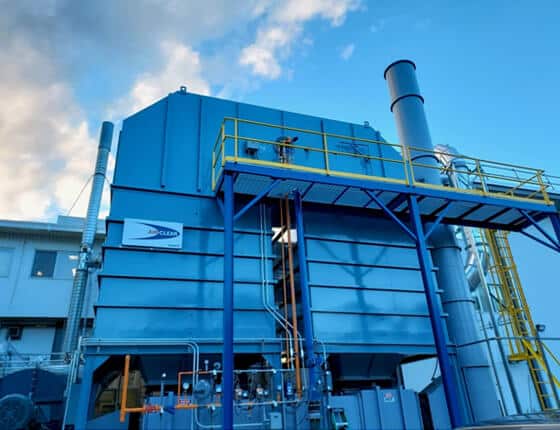
Air Clear’s 2 Canister RTO for St. Gobain in Hoosick Falls, NY
Components of an Air Clear
Regenerative Thermal Oxidizer (RTO)
- Ceramic heat recovery beds capture and reuse up to 95% of the systems energy, resulting in low fuel cost. Heat Recovery Media will be best determined after reviewing solvent constraints, utility costs, hourly usage and scheduling demands.
- Heat released from the oxidation of the VOCs is also captured in the heat recovery ceramic media beds. This further helps reduce supplement fuel use. With a VOC concentration of about 3% of the LFL, the ThermGen™ Regenerative Thermal Oxidizer (RTO) unit is self sustaining. No supplement heat input is required.
- Requirements for MACT, BACT, LAER and RACT make it the preferred oxidation technology for many applications.
- Highly effective at reducing VOCs by means of thermal oxidation.
- Eliminates as much as 99%+ of the VOCs, meeting the EPA requirements for MACT, BACT, LAER and RACT. This makes it the preferred oxidation technology for many applications.
- “In house” fabrication from controls to reactors insures our customers that Air Clear maintains quality and schedule control over their projects.
- Seamless interface between our customers process and the ThermGen™ RTO with PLC, tailored to the processes operation.
- Flexibility when selecting system components such as structured vs. random heat recovery media, burners vs. electric heating elements and carbon steel vs. alloy construction. We our customers the best of both worlds with proven technology custom tailored to their specific project conditions.
- Carbon steel vs. alloy construction gives our customers the proven technology they need, custom tailored to their specific project conditions.
- “Dirty” process streams are controlled using a variety of pre-filters and media Bake Clean option.
- FAT (Factory Acceptance Test) reduces commissioning and start up time by running a thorough diagnostic system check PRIOR to shipment.
- Air Clear has extensive knowledge of various materials of construction and metallurgy to insure long-term system performance and reliability, especially when working on Chlorinated applications. Air Clear has fabricated industrial RTO units from Hastelloy, ALX6N as well as 304, 316 SS.
- Air Clear’s quench/scrubbers are used to remove acids such as HCL, HbR H2SO4 formed during the oxidation reaction. Secondary Heat (energy) Recovery (SHR) systems can be added to provide for a positive payback from Air Pollution Control Equipment.
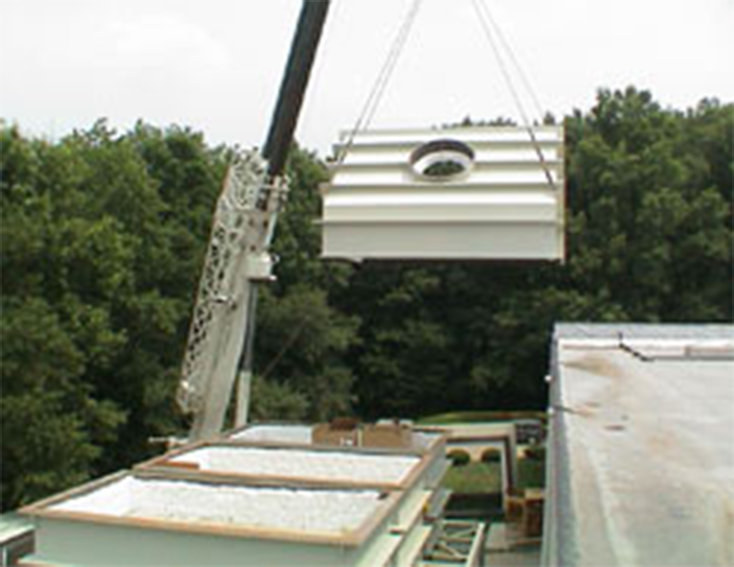
Ceramic Media Installed Prior to the top being installed on A 50,000 SCFM Regenerative Thermal Oxidizer (RTO)
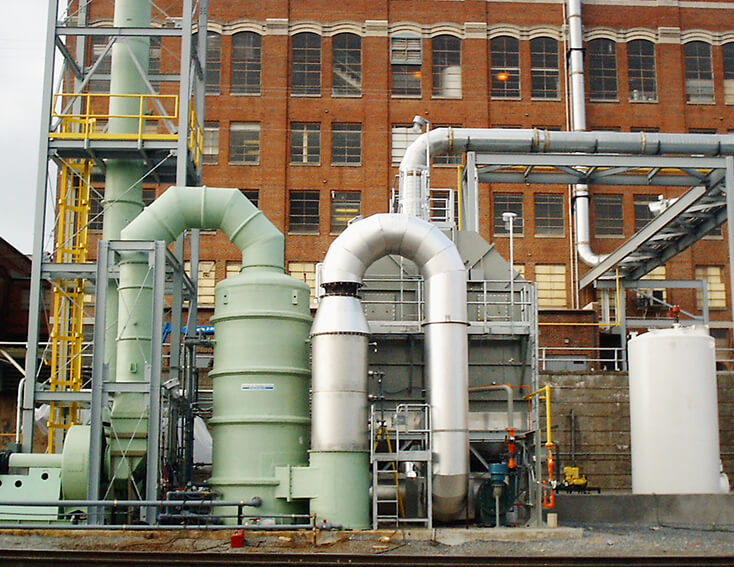
25,000 SCFM THERMAL REGENERATIVE OXIDIZER (RTO) WITH SCRUBBER ON CHEMICAL PROCESS
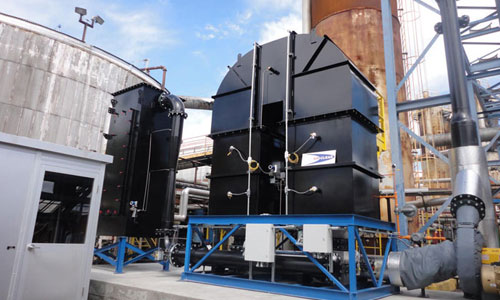
2,500 SCFM REGENERATIVE THERMAL OXIDIZER (RTO) WITH COALESCING FIBERBED FILTER MIST COLLECTOR SYSTEM ON ASPHALT ROOFING & SHINGLE PRODUCTION LINE.
Secondary Heat
Recovery (SHR)
In some cases, the waste heat from the hot combustion exhaust (which normally is vented to the stack), is recovered in a secondary heat recovery system. This results in additional energy savings. Contact Air Clear Engineers to analyze your project for secondary heat recovery feasibility.
SFI – Safe Fuel Injection can be used to lower fuel use further by eliminating supplemental combustion air needed for the burner.
Hot Bypass Valve (HBV)
In some cases, a Hot Bypass Valve is used to direct the clean (hot) oxidizer exhaust around the heat recovery bed, directly into the stack. Bypassing allows the Regenerative Thermal Oxidizers to tolerate higher solvent loads.
Insulation
A key design feature of the ThermGen™ Regenerative Thermal Oxidizers (RTO) is the use of high-density ceramic modules.
- A stainless steel frame supports each module, and the frames are individually welded to the inside of the combustion chamber. When the adjacent module is put into place, it generates lateral support by compression.
- The insulating modules are made from high purity ceramic fibers. The modules are constructed to prevent spalling or erosion of the fibers, which would normally result when the fibers expand in different directions when heated.
- Efficiency, durability, and low maintenance factors make the Air Clear insulating system a key component of the industrial RTO system.
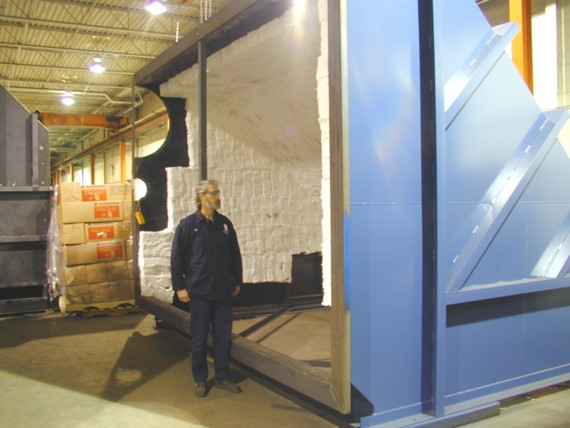
MASTIC COATING FOR REGENERATIVE THERMAL OXIDIZER COMBUSTION CHAMBER UNDER CERAMIC INSULATION.
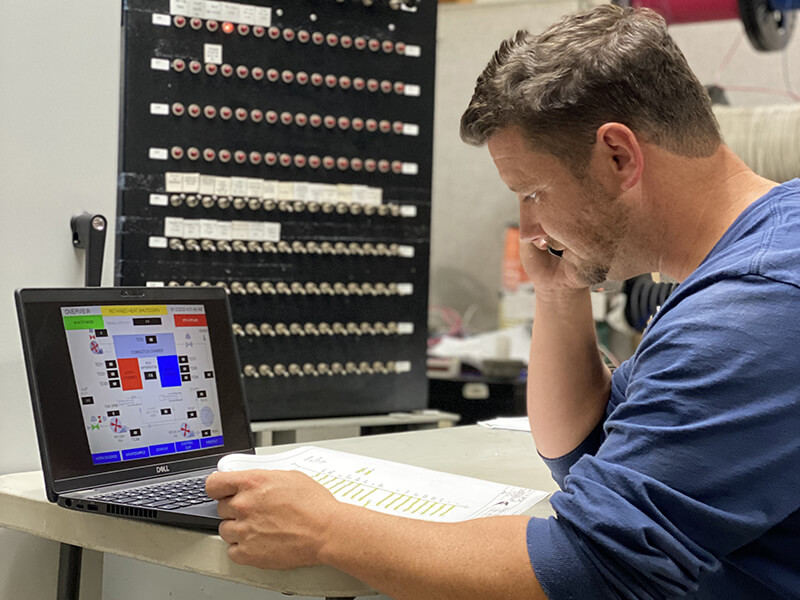
AS A SERVICE, AIR CLEAR OFFERS CUSTOMERS REMOTE MONITORING FOR TROUBLE SHOOTING OUR THERMAL OXIDIZER SYSTEMS
Programmable Logic
Controller (PLC)
PLC’s are available with input and output (I/O) options and electrical configurations that make them ideal for a wide range of applications.
Air Clear Engineers have experience with many PLC Manufacturers. Program Logic Controllers (PLC’s) provide the following advantages over relay logic control.
- Fast, specific diagnostics
- Easy data acquisition
- Easy operator use with various levels of access
Field Support
Field support is provided throughout the world on all of Air Clear Systems
- Complete Turnkey Service
- Remote Monitoring Services
- Engineering Services
- Pilot Testing
- Inspection Services
- Scheduled Maintenance Services
Sales Support
Field support is provided throughout the world on all of Air Clear Systems
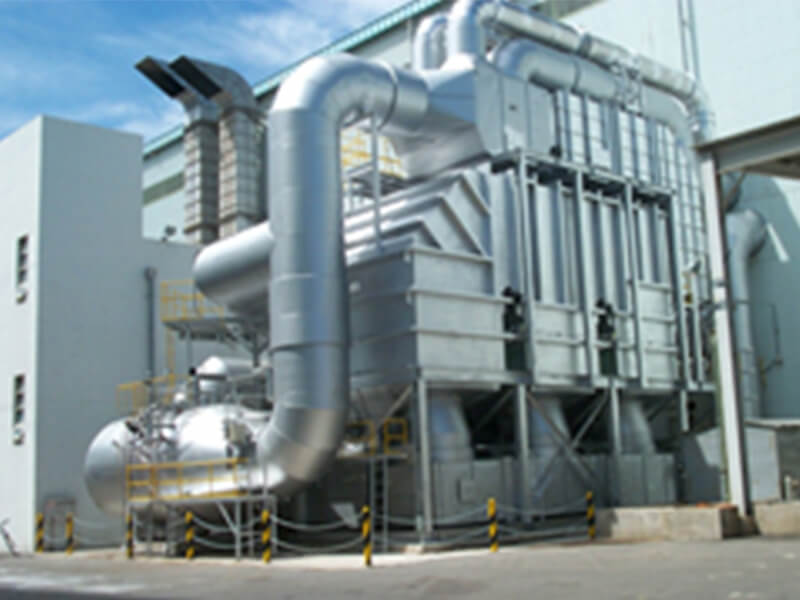
30,000 SCFM 3-CHAMBER STAINLESS STEEL REGENERATIVE THERMAL OXIDIZER (RTO), WITH HOT BYPASS VALVE & WASTE HEAT EXCHANGER & WASTE HEAT BOILER.
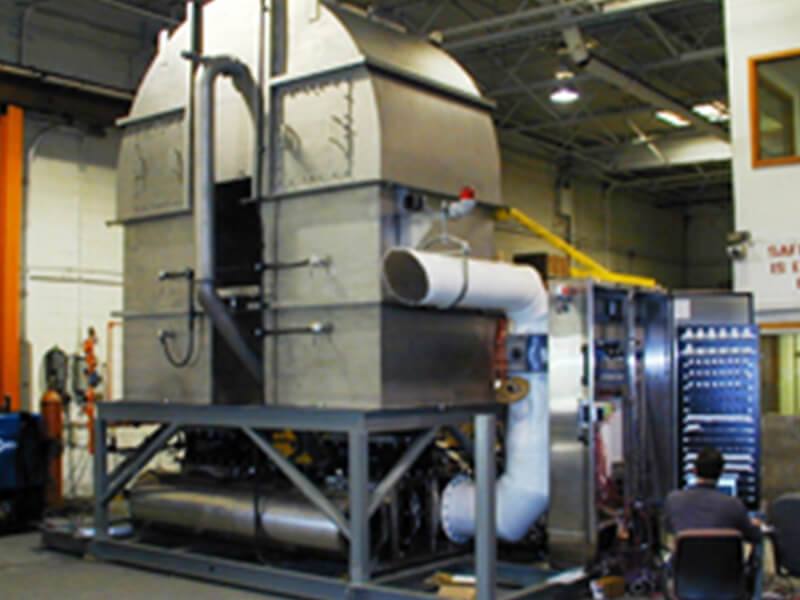
3,500 SCFM 2- CHAMBER REGENERATIVE THERMAL OXIDIZER (RTO) ON PHARMACEUTICAL MANUFACTURING PROCESS.
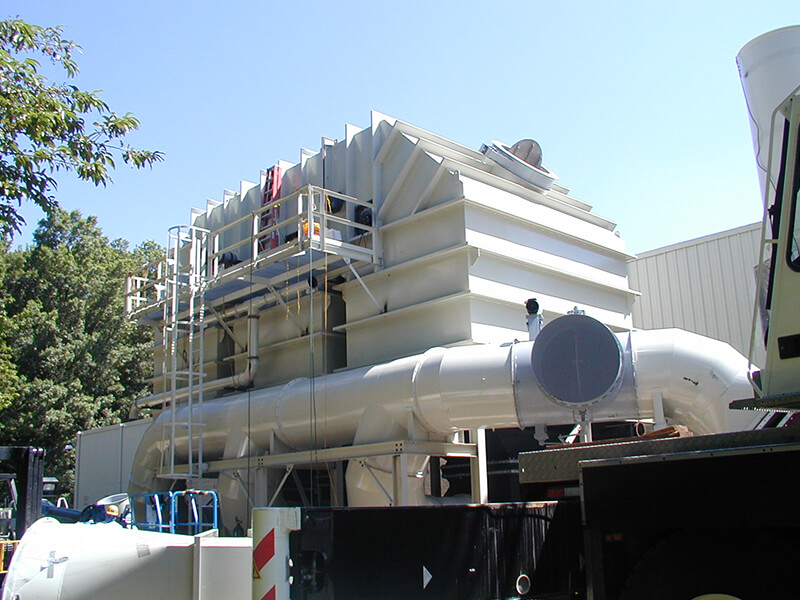
50,000 SCFM REGENERATIVE THERMAL OXIDIZER (RTO) ON SPECIALTY FILM PRODUCTION LINE.