Thermal Oxidizers can be applied to a wide variety of processes. They are often the technology of choice because of durability and adaptability over a wide range of operating conditions.
Today’s Air Pollution Control applications require the world’s most advanced thermal oxidizer systems to destroy hazardous air pollutants (HAPs) and volatile organic compounds (VOCs) while meeting or exceeding tougher environmental regulations.
The Air Clear Recuperative Thermal Oxidizer combustion designs a broad range of Thermal Oxidation Systems to effectively destroy a wide variety of hazardous industrial wastes with destruction efficiency up to 99.99%, all while protecting the environment. We work closely with customers to develop clean-combustion systems that incorporate proven technology solutions. Recuperative Thermal Oxidizers have been used for many years as a straightforward and effective means of destroying organic fumes in process exhaust gas.
Why the Air Clear Thermox™
Recuperative Thermal Oxidizer
- Proven technology for oxidation of volatile organic compounds (VOCs) and for the control of odorous emissions with greater than 99.99% efficiency!
- Recognized as the Best Available Control Technology (BACT) and Maximum Control Technology (MACT) for many industrial process.
- Thermox™ Recuperative Thermal Oxidizers reduce energy costs by using a pre-heater (heat exchanger) to recover the heat from the post oxidized air to preheat the incoming process air, further savings can be gained with a secondary heat recovery or “economizer” Recuperative – meaning to recover and restore.
- The Thermox™ Recuperative Thermal Oxidizer is designed to provide reliable stable operation over a wide range of process conditions.
- Small or large flows as well as multiple sources feeding one thermal Oxidizer can utilize thermal oxidation to control emissions. The Thermox™ Recuperative Thermal Oxidizer is also an excellent choice for intermittent ON-OFF use.
- Direct-fired thermal oxidizers can rapidly adjust to changes in VOC loadings. When equipped with a High Temperature Bypass Valve (HTBV).
- Flexibility – Custom design-meets your specific project objectives at the lowest cost possible.
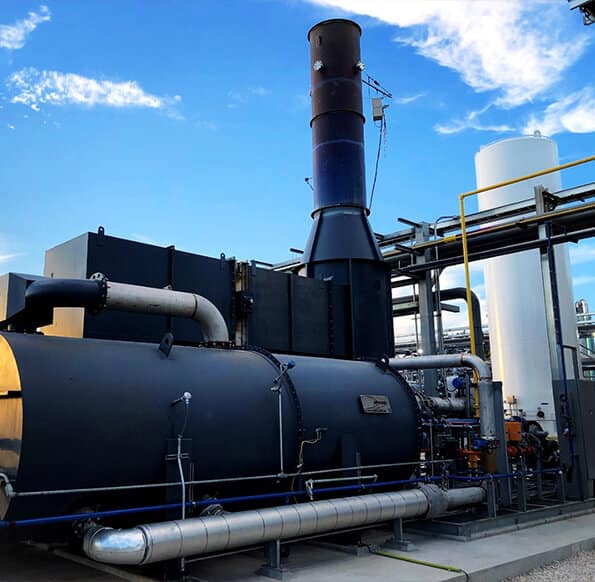
This Direct-Fired Thermal Oxidizer (THERMOX) with Quench and HCL Scrubber
Scrubber is for Solvay Chemicals in Princeton, NJ designed for treatment on a mud still exhaust emission source stream
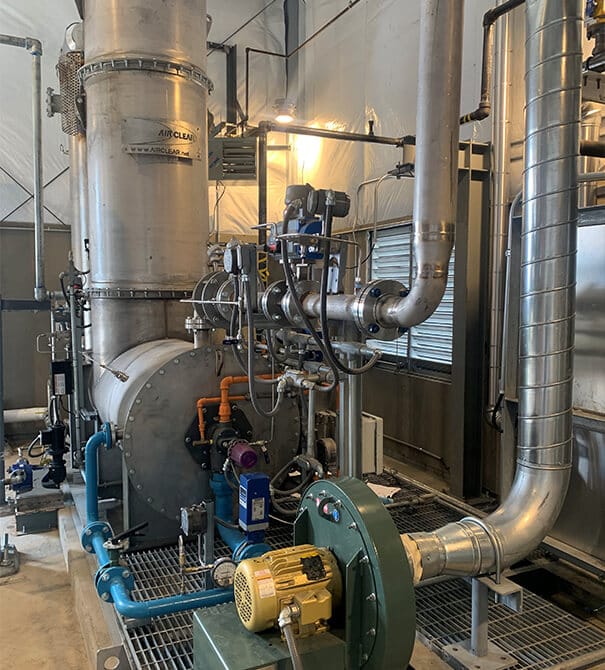
Recuperative Thermal Oxidizers (TOXs) are different from Regenerative Thermal Oxidizers (RTOs) Very simply put, Recuperative is a normal Thermal Oxidizer with an air-to-air Heat Exchanger (HXT) at the outlet to recover some of the heat normally lost to the exhaust. Whereas Regenerative is referring to the process of how the heat “regenerated” using specially engineered high-temp ceramic media using the outlet exhaust gas in a more complex style of equipment that is also using Thermal Oxidation.
If you’re wondering what is the difference between a Direct-Fired Thermal Oxidizer (TOX) and a Recuperative Thermal Oxidizer (TOX) vs (TOX) A Recuperative Thermal Oxidizer is a Direct-Fired Thermal Oxidizer with a Heat Exchanger. The Direct-Fired Thermal Oxidizers are the more common of the two. A classic Direct-Fire Thermal Oxidizer THERMOX efficiently react the hydrocarbons (HC), volatile organic compounds (VOCs) and hazardous air pollutants (HAPs) with oxygen in the air to form naturally occurring carbon dioxide and water vapor (HC + 02 + heat >H20 + CO2). This reaction occurs when the air is heated to a sufficiently high temperature, typically 1400-1600 F. The fuel needed to heat the process stream to the oxidation temperature is greatly reduced in a THERMOX Recuperative Thermal Oxidizer system by using a Recuperator or “preheater" but in this case that isn’t present so it is a Direct-Fired Unit. With or without a preheater, the THERMOX is capable of achieving the highest VOC, hydrocarbon, and odor destruction of any of our technologies. The THERMOX is also designed to provide reliable performance over a wide range of process variables, ensuring our customer’s compliance.
Best Value
Air Clear relies on a network of world class providers of specialty components selected by our Engineers for integration into cohesive system. Suppliers are selected based on the design features, quality of construction, and cost competiveness. In addition, Air Clear fabricates internally, eliminating the cost mark ups passed on by subcontracted fabricators.
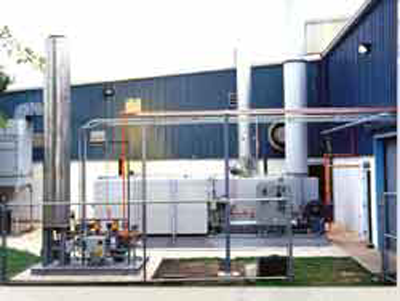
5,000 SCFM Recuperative thermal oxidizer with shell and tube heat recovery system on coating process.
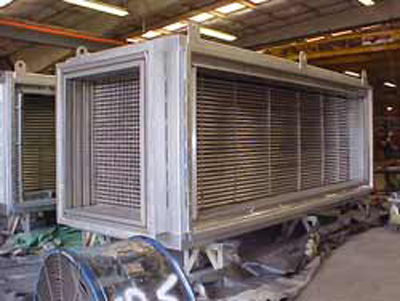
10,000 SCFM Shell & tube heat recovery system for recuperative thermal oxidizer.
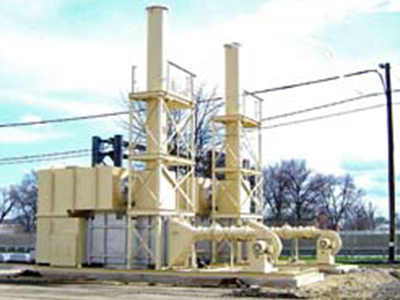
12,500 SCFM Skid mounted recuperative thermal oxidizer with primary heat recovery system on soil vapor extraction process.

5,000 SCFM Skid mounted recuperative thermal oxidizer with primary heat recovery system.
Post
Commissioning Support
Worldwide Capability- AC has completed projects worldwide. Air Clear supports these projects on an ongoing basis by a combination of in house resources, remote diagnostics and localized support personnel.
FAT – Factory Acceptance Test – reduces commissioning and start up time by running a thorough diagnostic system check PRIOR to shipment
Air Clear has extensive knowledge of various materials of construction and metallurgy to insure long-term system performance and reliability, especially when working on Chlorinated applications
How Air Clear Thermox™
Recuperative Thermal Oxidizers Works
- Prior to ignition, the air inside the oxidizer must be purged to extract any residual gas that may have leaked into the chamber. The purge is controlled with a timer; this insures the proper volume of fresh air. The blower, in conjunction with an ambient air valve, forces clean air through the system. To prevent the possibility of drawing additional contaminated air from the process, an isolation valve closes off the process and permits ambient (fresh) air to enter the system.
- Requirements for MACT, BACT, LAER and RACT making it the preferred oxidation technology for many applications.
- Upon completion of the system’s purge, the gas blocking valve opens and the burner pilot is ignited, and the main gas blocking valves open allowing the oxidizer to reach the operating temperature.
- Contaminated process air is forced (pushed) into the thermal oxidizer by means of a centrifugal blower or in some cases, as a result of a positive process pressure.
- As the contaminated process air moves into the heat exchanger (pre-heater), the process gas is heated by means of the hot exhaust gas exiting from of the combustion chamber.
- The preheated air then enters the combustion zone. The air temperature must be raised to the required oxidation temperature, usually between 1,400-1,600 F. The additional heat that is required to reach the oxidation temperature is provided by a burner using supplemental fuel such as natural gas, propane, oil or liquid organic wastes. Preheating of the contaminated air in the pre-heater heat exchanger can greatly reduce the amount of supplemental fuel required.
- The combustion chamber (reactor) is sized to provide the required residence time, which will allow for the desired conversion efficiency. The reactor is internally insulated with high temperature ceramic fiber module to conserve heat. In general AC Systems have exterior temperatures which average less than 150 F
- The oxidation reaction breaks down the Hydrogen / Carbon bonds using heat energy. In the presence of oxygen, the result is reformed products, namely Carbon Dioxide (CO2) and water vapor (H2O) a typical reaction using toluene as (C7 H8 + 9O2 + Heat -> 7CO2 + 4H2O+ exotherm).
- The post-oxidized air passes on the opposite (clean) side of the preheat heat exchanger. The clean and dirty sides of the exchanger passages are completely isolated, preventing mixing or cross contamination of the incoming and outgoing air streams.
- The hot, post-oxidation gas flows in an opposite direction to the incoming air. As the two streams pass each other, heat from the post-oxidized “clean” air is transferred to the cooler incoming process air.
- As the “clean” air exits the heat exchanger, it passes through the exhaust stack before being released to atmosphere.
- In some cases, there is a need to recover the remaining waste heat energy for process, building heat or steam. In these cases, a secondary heat exchanger, often referred to as an economizer, is used to recover even more of the heat from the oxidized exhaust. In its simplest form, a pair of dampers works together to direct all or some of the hot exhaust from the stack to the secondary heat exchanger. Clean ambient air flows across the other side of the exchanger, heating the clean air for process or building heat. The two streams are isolated, eliminated any potential mixing or cross contamination.
- In combination, the pre-heater and VOC’s heat output can often provide more heat than is needed to maintain the oxidation temperature. In these cases, a High Temperature Bypass Valve (HTBV) is used to direct the clean, hot oxidizer air around the heat exchanger, rather than allowing it to go through the pre-heater.
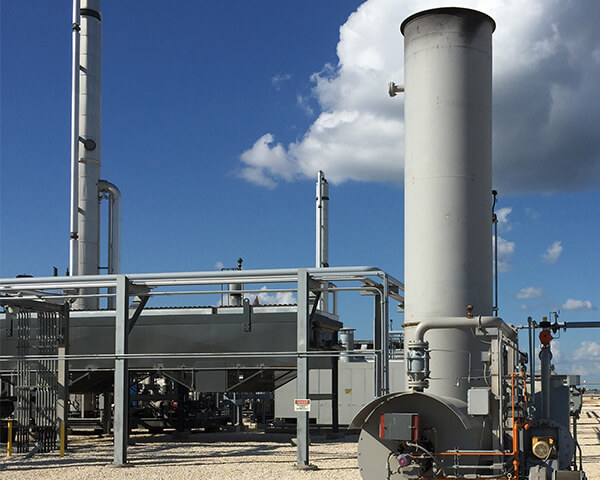
Direct Fired Thermal Oxidizer on a loading station
Direct Fired Thermal Oxidizers (which do not utilize primary forms of heat recovery to lower fuel consumption) are the simplest straight forward type of thermal oxidizer. Direct Fired Thermal Oxidizers are also known as Afterburners, DFTO’s, Fume Incinerators, and Enclosed Flares. Over the years, advances in heat recovery equipment has reduced the applications that utilize Direct Fired Oxidizers.
However, the simplicity of operation, ability to achieve very high DRE (destruction removal efficiency), ability to be online and accepting process quickly, and tolerance for varying VOC loadings have opened new opportunities for direct fired units. Air Clear has recently supplied Direct Fired Thermal Oxidizers for applications in the Oil and Gas industry (include truck and terminal loading facilities), Ethanol Plants, Carbon Fiber, Coating and Chemical Processing.
Also, our proprietary design for Renewable Natural Gas or Landfill Gas to pipeline grade uses our advanced burner systems to process waste streams which are made up of 25% Methane. Air Clears’ tank degassing/cleaning oxidizers (mobile or stationary) achieve 99.99% DRE! When the utilization of waste heat recovery is added to the system making a DFTO a cost effective solution.
Program Logic
Controllers
The controls must insure the safe operation of the thermal oxidizer and also integrate the thermal oxidizer’s operation into the operation of the process. NFPA code requires specific control features, such as pre-ignition purge and flame identification.
Air Clear Engineers have experience with many PLC Manufacturers. PLC’s provide the following advantages over relay logic control.
- Fast, specific diagnostics
- Remote monitoring
- Easy data acquisition
- Easy operator use with various levels of access
- Interfaces/integrates easily with process operations
- Cost effect in most applications are available with input and output (I/O) options and electrical configurations that make them ideal for a wide range of applications
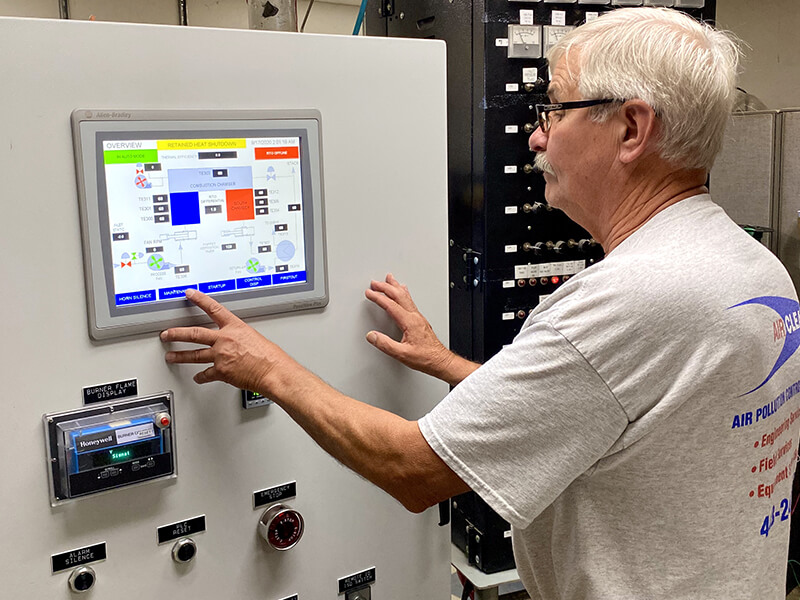
PROGRAMMING OF AIR CLEAR THERMAL OXIDIZER CONTROL PANEL
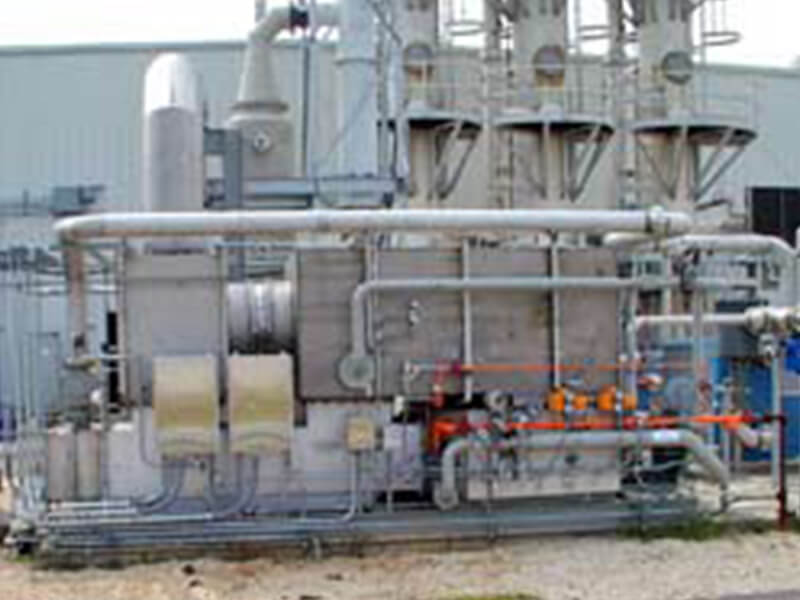
RECUPERATIVE THERMAL OXIDIZER FOR SOIL VAPOR REMEDIATION PROJECT
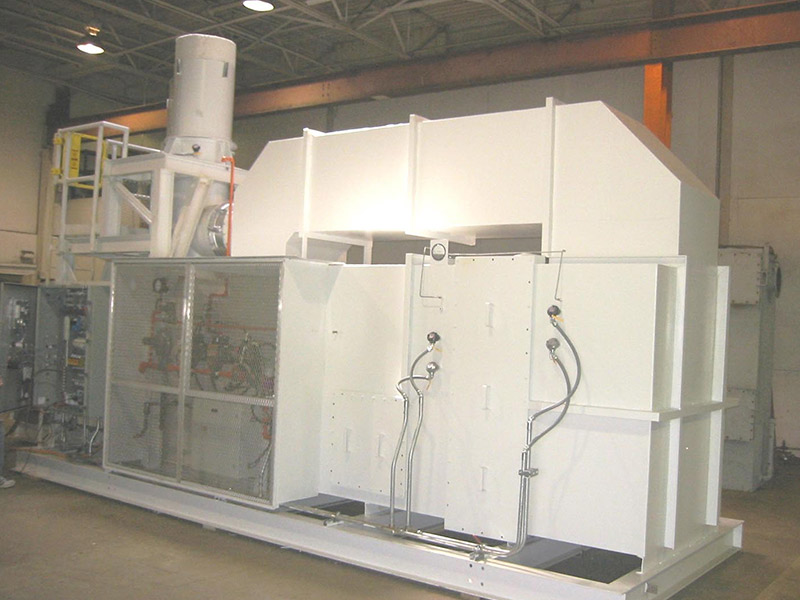
5,000 RECUPERATIVE THERMAL OXIDIZER WITH PRIMARY AND SECONDARY HEAT RECOVERY.
StanChem Polymer’s East Berlin, CT location
This work in progress was manufactured by our talented fabrication team here at our Elkton, MD facility. This particular unit is a THERMOX unit, commonly known as a Direct Fired Thermal Oxidizer. Its 380scfm, with a destructive efficiency of all harmful process VOCs that is over ≥99%. At Air Clear our goal is to create a cleaner world where businesses can thrive economically without damaging the environment, we all share. We strive to provide our clients with the most current and efficient solutions for emissions control at affordable prices that stay within their budget while never requiring the sacrificing of quality.
As a society, we continue to move toward more sustainable development and that is something intrinsic at Air Clear. The tenets of sustainability require that we focus not only on the environmental factors, but economic and social ones as well. It seems to all come back to longevity through quality design and fabrication. Providing our clients with confidence that when they come to Air Clear they are consistently getting the highest quality product at the lowest possible price and always outperforming expectations.
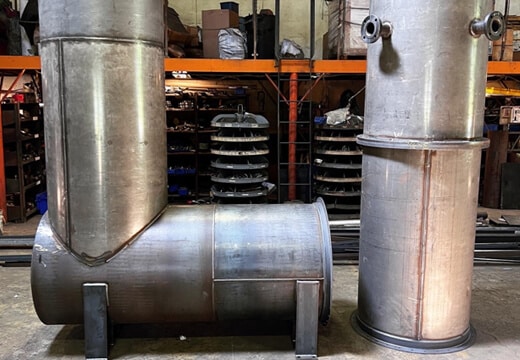
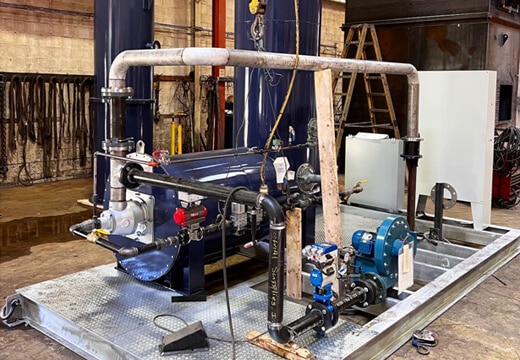
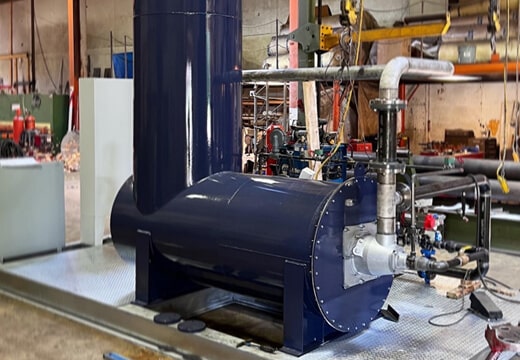
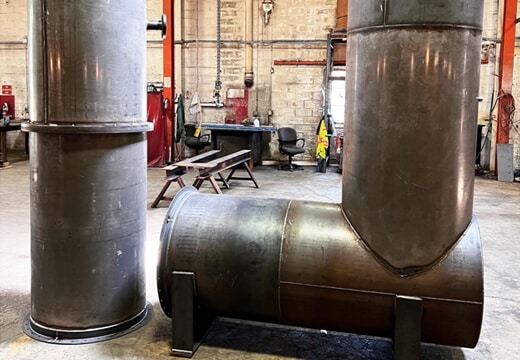