Client:
Envita for Large Noodle Manufacturer, whose name is confidential.
Location:
South Korea
Background:
Emissions from eight noodle ovens were causing visible emissions and also oil/grease pollution coating on the roof around the exhaust stacks. Air Clear compared two oil mist control technologies: Regenerative Thermal Oxidizer (RTO) and Fiberbed Mist Collector. The cost advantage was clearly in favor of the industrial Oil Mist Collector, however, the end user wanted to see performance as this was the first application of the Oil Mist Collector on a noodle manufacturer. The three month Pilot Test demonstrated that the Mist Collector removed greater than 99% of all oil aerosol particulate greater than 0.1 micron and larger.
Waste Description:
Oil and grease aerosol mist from hot peanut, coconut and vegetable oils.
Solution:
Air Clear installed 530 3/minute (18,500 ACFM) Fiberbed Filter Mist Collector System to remove the submicron particulate that was causing the opacity ‘smoke’ problem. To protect against solid particulate and to protect the unit from duct fires a cyclonic water scrubber was used to remove the solids and to provide a water seal which would serve as a fire block in case of a duct fire. In addition to greatly reducing odors, the Air Clear Fiberbed Filter Mist Collector provided zero visible emissions.
A steam pipe was connected to the shell of the oil mist removal unit to heat the coalescing filters and restore the pressure drop. This allowed the filters to last for several years.
Process Equipment:
Eight oven stacks were duct together creating one inlet duct to the industrial Oil Mist Collector. Any number of units, one to eight, can exhaust to the Mist Collector by using isolation dampers on each line. A VFD was also used to control the flow from the ovens to the Oil Mist Collector.
Case Study
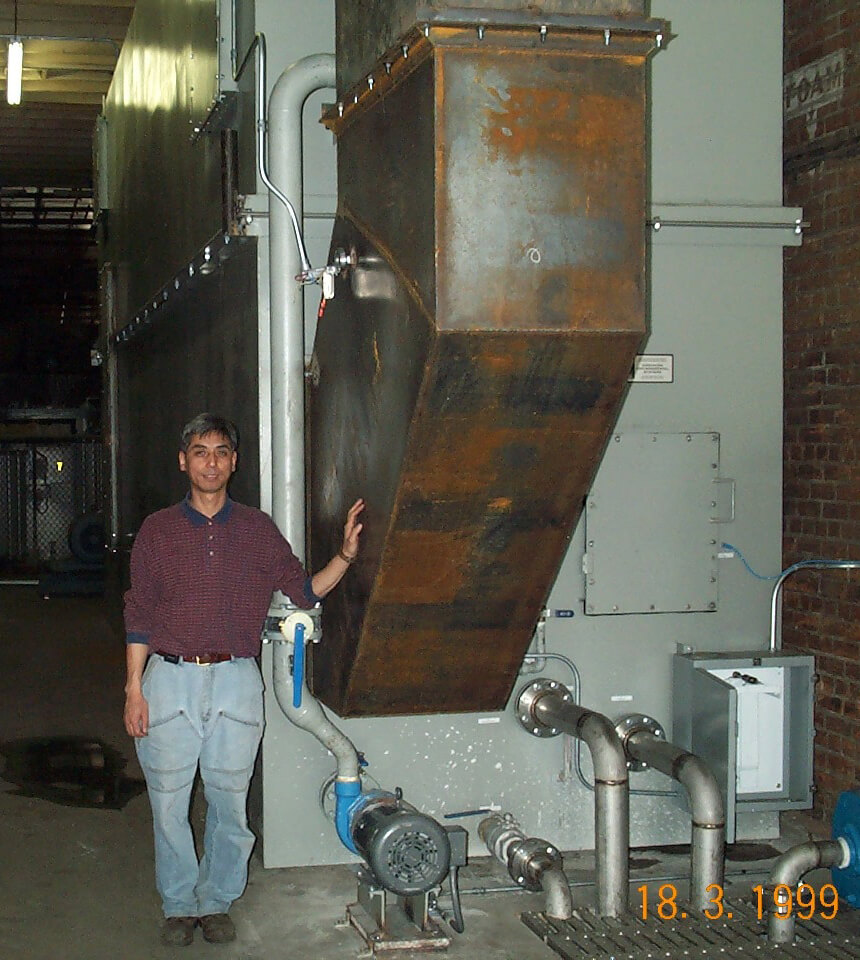
Air Clear Fiberbed Filter Mist Collector System controls emissions from Large Noodle Manufacturing Process in South Korea